The Heart Guardian of Plastic Extrusion Lines: A Practical Guide to Selecting and Maintaining Single-Screw Reduction Gearboxes
03
2025-06
"Amidst the thunderous clamor of plastic single-screw extruders, there exists one vital component that quietly undertakes the most demanding responsibilities yet frequently remains in the shadows—the reduction gearbox."
Don’t underestimate this unassuming iron lump; it’s the "power heart" and "torque amplifier" of your entire production line. While motors spin rapidly, extruder screws demand slow, forceful rotation. The gearbox is this critical energy converter. Choose wrong or neglect maintenance? The price could be hours—even days—of downtime, six-figure repair bills, and your boss’s deep frown.
Today, we delve into this "silent hero" guarding your production efficiency and profits.
I. The Gearbox: Far More Than Just Speed Reduction
Novices might see gearboxes as mere speed-reducing boxes. But in plastic extrusion’s high-pressure, high-temperature, high-load environment, they’re the cornerstone:
Birth of a Hercules:
Motors deliver high speed but low torque. Imagine forcing a 100mm+ screw to compact tons of icy pellets, melt them, and pump molten plastic through a die under extreme pressure. The gearbox’s mission? Amplify the motor’s "strength" into the colossal force (high torque) the screw demands.
Pillar of Stability:
Erratic screw speed = fluctuating melt pressure = uneven thickness, unstable dimensions, soaring defect rates. A precision gearbox ensures steady rotation—the bedrock of product consistency.
"Pressure Warrior":
When processing high-viscosity materials (e.g., rigid PVC) or high-fill compounds (e.g., calcium powder, fiberglass), startup jams or flow disruptions unleash massive resistance. Gears, bearings, and housings must withstand these impact loads like bedrock—never compromising.
II. Choosing the Right "Heart": Avoid Pitfalls, Save Big!
Selecting gearboxes isn’t about cheap prices or "close enough" specs. "Close enough" here means "disastrously inadequate"! Years of industry experience dictate these non-negotiable criteria:
"Muscle" Matters (Torque):
The core parameter! Don’t just eye motor power—calculate your screw’s peak torque demand under worst-case scenarios (cold startups, high-fill processing). Critical tip: Multiply calculated torque by ≥1.5x safety factor (SF). Undersize to save money? Brace for gear-grinding screams! (*Real-world lesson: A client saved $20k on a gearbox but lost $200k in downtime 6 months later.*)
Precision "Pacing" (Reduction Ratio):
Screw’s max RPM? Motor’s rated RPM? Their ratio defines the reduction ratio. Match it to ensure output speed meets process needs.
"Physique" Requirements (Construction):
Gear Type: Helical gears dominate—smoother, quieter, stronger than spur gears. For ultra-precision (e.g., medical tubing), invest in double-helical gears; they cancel axial thrust and last longer.
"Skeleton" Rigidity (Housing): Cast iron or welded steel is essential. Weak housings deflect under load, misaligning gears and accelerating wear.
"Joint" Durability (Bearings): Use heavy-duty bearings (typically tapered roller combos) that handle radial AND axial loads. Cheap/small bearings = early failure.
"Temperature" Control (Cooling): Gear friction + barrel heat make gearboxes "feverish." High-power units must have forced lubrication + oil coolers (air/water). Small units need ample cooling fins.
"Blood Flow" Assurance (Lubrication): Reliable pumps, filters, and oil/temp monitors are non-negotiable for large gearboxes. Filters aren’t optional—they stop metal debris from murdering gears/bearings!
III. Field Selection Checklist: 7 Critical Questions
Screw size? (Diameter = torque determinant)
Max screw RPM? (Sets reduction ratio)
Motor power (kW/HP) & speed?
"Worst abuse" scenario? (Processing rigid PVC pipes? 50% glass-filled nylon? Material dictates torque!)
Workshop environment? (High temp? Dusty? Humid?)
Daily runtime? (8hr vs. 24/7?)
Budget & lifespan target? ("Just works" vs. "10-year beast"?)
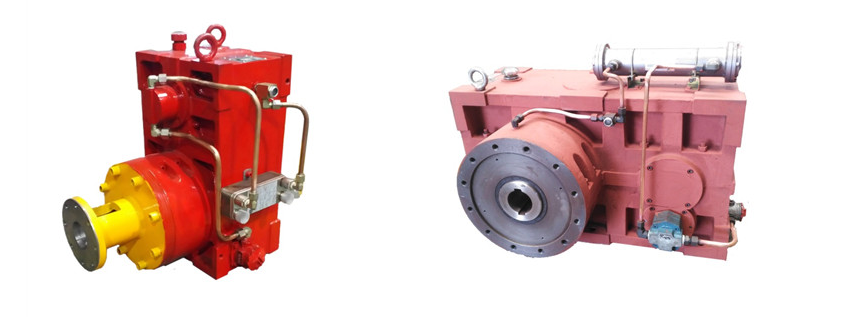
Specifications:
Model | ZLYJ 112 | ZLYJ 133 | ZLYJ 146 | ZLYJ 173 | ZLYJ 200 | ZLYJ 225 | ZLYJ 250 |
Kw Power | 5.5-4P | 8-4P | 11-4P | 18.5-4P | 26-4P | 45-4P | 45-4P |
ratio | 8 | 8 | 10 | 10 | 12.5 | 12.5 | 16 |
Screw | Φ35 | Φ45/50 | Φ55 | Φ65 | Φ75 | Φ90 | Φ100 |
Model | ZLYJ 280 | ZLYJ 315 | ZLYJ 330 | ZLYJ 375 | ZLYJ 420 | ZLYJ 450 | ZLYJ 560 |
Kw power | 55-6P | 75-6P | 132-6P | 132-6P | 160-6P | 213-6P | 440-6P |
Features:
1.The gear has the advantages of high precision and good meshing performance.
2.The box body is an integrated design.
3.The box material is ductile iron with high quality.
4.The box has the advantages of high strength and beautiful appearance.
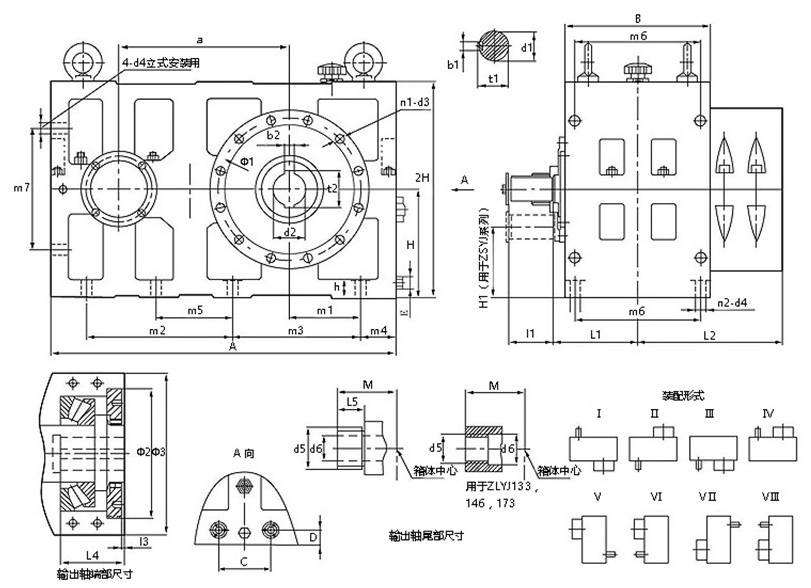
IV. Maintenance: Your "Life-Extending Gospel" – Don’t Wait for Failure!
Even top-tier gearboxes fear "abuse." Neglect is their #1 killer. Heed these survival rules:
"Blood" = Life (Lubricant):
Right Oil: Strictly use manufacturer-specified type/viscosity! Wrong oil = slow suicide. (Case: A plant used cheap oil → insufficient film strength → pitting in 6 months.)
Timely Changes: Stick to scheduled oil/filter replacements. Harsh environments? Change earlier!
Oil Analysis: Regularly test for metal particles, water, viscosity shifts. This "X-ray" predicts failures—tiny cost, massive savings!
"Breathing" Matters (Vents/Filters): Replace breather filters to block dust/moisture contamination.
Monitor "Fever" (Temperature): Install sensors on bearings/oil. Sudden spikes? Investigate NOW!
"Bone Alignment" (Shaft Coupling): Laser-align motor-gearbox-screw during install/post-maintenance. Misalignment = vibration + noise + murdered bearings.
Daily "Stethoscope" Checks: Experienced techs use listening sticks/vibration pens to catch abnormal noises/vibration—your earliest failure alarm.
Advantages:
1.The gearbox use different bearings and it takes into account the reliability and economy of the product.
2.Our company has advanced equipment such as Gleason forming gear grinding machine.
3.Our company has a special testing center.
4.Our company has convenient transportation, located in Beijing Shanghai high-speed and high-speed along the River Interchange Qiaoqi exit.
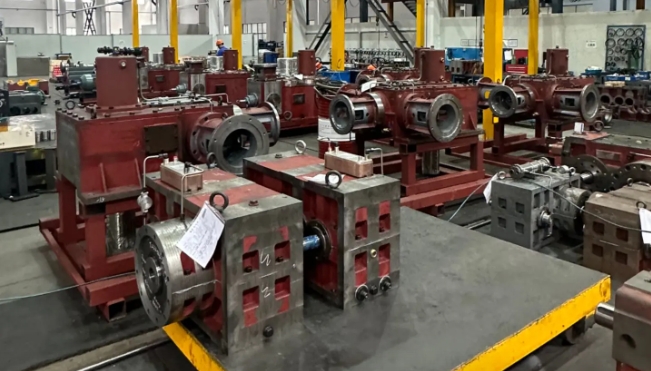
V. Brands & Service: Look Beyond Price – Who’s Got Your Back?
A gearbox purchase = long-term security. Prioritize:
Experience Rules: Choose manufacturers specialized in extrusion gearboxes with deep plastics industry roots. They get your pain points.
"Hard Power" Talks: Scrutinize gear steel grades (e.g., 20CrMnTi carburized), bearing brands (SKF/FAG/TIMKEN?), and grinding precision. Materials/processes define longevity.
Service Network: When your gearbox crashes at midnight, can they respond? Local support/spare parts? This dictates downtime costs.
Customization Power: Unique needs? Retrofits? Top players deliver tailor-made solutions.
Applications:
1.The gearboxes are widely used in plastic machinery, plastic industry, environmental protection industry, building materials, electric power, steel, mine, metallurgy, coal, petrochemical, port transportation, municipal construction and many other fields.
2.The experience of countries all over the world shows that the more developed the economy, the greater the consumption of plastic products. Plastic extrusion industry cannot do without gearbox, as an important part of power supply.
3.DELING gearboxes can equipped with PVC/WPC foam board production line, PVC/WPC flooring production line, PVC imitation Marble sheet/profile production line, PVC wall panel production line, WPC production line.
In plastic extrusion’s margin-tight world, unplanned downtime is the ultimate profit killer. A properly sized, meticulously maintained reduction gearbox is the unsung hero ensuring continuous, stable, efficient production. It operates silently yet decides whether you:
✅ Deliver orders on time
✅ Produce premium-quality goods
✅ Control maintenance costs vs. financial meltdowns
Don’t gamble with your extrusion heart!
→ Prioritize precision selection.
→ Invest in proactive maintenance.
→ Partner with gearbox guardians who stand by you 24/7.